In the realm of modern construction, the integration of robotic welding and fabrication technologies has ushered in a new era of efficiency, precision, and innovation. With the global construction industry projected to reach a value of $10.5 trillion by 2023, according to data from Statista, the demand for advanced fabrication methods has never been greater. Construction Robots have emerged as game-changers, offering unparalleled capabilities in welding, cutting, and material handling, thereby revolutionizing traditional construction practices.
As we delve into the myriad applications and benefits of robotic welding and fabrication in construction, it becomes evident that these technologies are not merely futuristic fantasies but tangible solutions driving tangible results. From towering skyscrapers to intricate architectural marvels, robotic systems are leaving their indelible mark on construction projects of all scales and complexities.
Arc welding robots, with their versatility and precision, have become indispensable for fabricating structural steel components with unmatched efficiency. Spot welding robots, renowned for their speed and consistency, are revolutionizing the assembly of sheet metal components, while laser welding robots offer unparalleled accuracy and aesthetic appeal in architectural metalwork.
Furthermore, plasma-cutting robots are transforming the way metal materials are cut, providing clean, precise cuts in a fraction of the time it takes with conventional methods. With each advancement in robotic technology, construction companies are empowered to streamline processes, enhance productivity, and deliver projects of exceptional quality within tighter timelines and budgets.
As we embark on this exploration of robotic welding and fabrication in construction, we witness firsthand the transformative power of innovation, shaping the future of the built environment one weld at a time.
Table of Contents
Top Robotic Welding and Fabrication Types in Construction
In construction, robotic welding and fabrication play a significant role in improving efficiency, precision, and safety. There are several types of robotic welding and fabrication methods commonly used in construction:
1. Arc Welding Robots
Arc welding robots are a prevalent type of robotic welding used extensively in construction due to their versatility, precision, and efficiency. Here’s a deeper dive into their characteristics and applications:
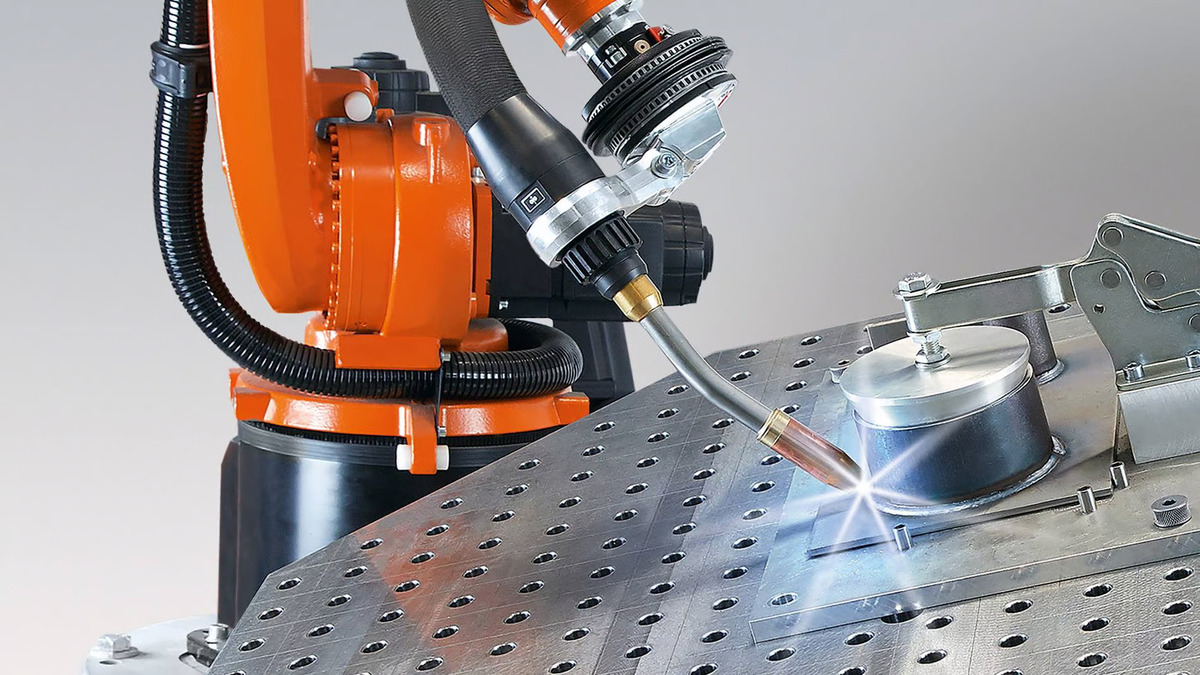
Characteristics:
- Versatility: Arc welding robots are adaptable to various welding processes, including Metal Inert Gas (MIG), Tungsten Inert Gas (TIG), and Stick welding. This versatility allows them to handle a wide range of welding tasks in construction, from joining structural steel components to fabricating metal panels.
- Accuracy: These robots can precisely control the welding torch position, angle, and speed, ensuring consistent and high-quality welds. This accuracy is crucial for maintaining the structural integrity and safety of construction projects.
- Efficiency: Arc welding robots operate at high speeds, leading to increased productivity and shorter production cycles. They can work continuously without the need for breaks, resulting in faster completion of construction tasks.
- Automation: Arc welding robots are fully automated, reducing the need for manual labor in welding processes. This automation minimizes human error, improves workplace safety, and allows skilled welders to focus on more complex tasks.
- Integration: These robots can be integrated into robotic welding cells or production lines, seamlessly working alongside other automated machinery and processes. They can also be programmed to communicate with other systems, such as CAD/CAM software, for precise weld path planning and optimization.
Applications in Construction:
- Structural Steel Fabrication: Arc welding robots are extensively used in the fabrication of structural steel components for buildings, bridges, and other infrastructure projects. They can weld beams, columns, trusses, and other steel elements with high precision and efficiency.
- Pipe Welding: In construction projects involving pipelines or plumbing systems, arc welding robots are employed to weld metal pipes together securely. These robots ensure leak-proof joints and consistent weld quality, meeting strict industry standards.
- Metal Fabrication: Arc welding robots play a crucial role in fabricating metal panels, frames, and assemblies used in architectural features, façades, and interior structures of buildings. They can handle complex geometries and join metal components with tight tolerances.
- Repair and Maintenance: Arc welding robots are also utilized for repair and maintenance tasks in construction, such as repairing structural steel components or reinforcing weakened structures with additional welds. Their precision and reliability make them valuable assets for prolonging the lifespan of buildings and infrastructure.
Overall, arc welding robots are indispensable tools in modern construction, offering efficiency, precision, and automation capabilities that help streamline welding processes and enhance the quality of construction projects.
Suggested article to read: Automation in Construction: A Guide to 2024
2. Spot Welding Robots
Spot welding robots are a vital component of automated welding processes in construction, particularly in applications requiring the joining of sheet metal components. Here’s a closer look at their characteristics and applications:
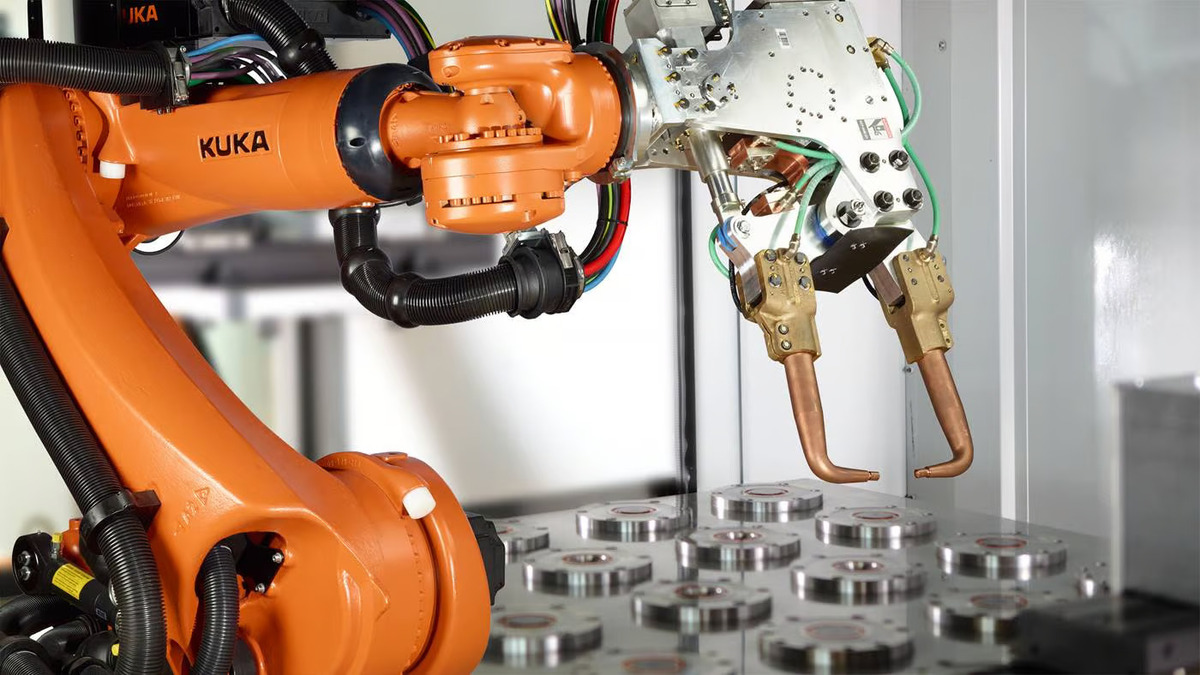
Characteristics:
- Localized Heating: Spot welding robots apply localized heat and pressure to specific points on metal sheets, creating welds by melting and fusing the materials together. This method minimizes heat distortion and preserves the integrity of surrounding areas, making it ideal for thin metal sheets commonly used in construction.
- High Speeds: Spot welding robots can operate at high speeds, enabling rapid production cycles and increased throughput in construction fabrication processes. Their ability to perform multiple welds in quick succession enhances overall efficiency.
- Consistency: These robots offer precise control over the welding parameters, ensuring consistent weld quality across all joints. This consistency is essential for maintaining structural integrity and meeting stringent construction standards.
- Adaptability: Spot welding robots can be programmed to accommodate various sheet metal thicknesses, shapes, and configurations. They can adjust welding parameters such as current, duration, and electrode force to suit specific welding requirements.
- Automation: By automating the spot welding process, these robots reduce reliance on manual labor, minimize human error, and improve workplace safety. Skilled welders can oversee operations and focus on more complex tasks, while the robots handle repetitive welding tasks efficiently.
Applications in Construction:
- Sheet Metal Fabrication: Spot welding robots are widely used in the construction industry for fabricating sheet metal components such as panels, ductwork, enclosures, and roofing materials. They can quickly join metal sheets together to create sturdy and durable assemblies required for building structures.
- Prefab Construction: In prefabricated construction methods, spot welding robots play a crucial role in assembling pre-made components and modules. These robots ensure precise and reliable welds, facilitating the rapid assembly of prefabricated elements at construction sites.
- Automotive Construction: Spot welding robots are also utilized in the construction of vehicles and transportation infrastructure, including automobiles, buses, trains, and railway components. They can weld automotive body panels, chassis components, and structural frames with high accuracy and efficiency.
- Appliance Manufacturing: Spot welding robots are commonly employed in the production of household appliances such as refrigerators, washing machines, and ovens. They can weld metal housings, cabinets, and internal components, contributing to the assembly of durable and reliable appliances.
Overall, spot welding robots offer construction companies a versatile and efficient solution for joining sheet metal components with precision and reliability. Their ability to automate repetitive welding tasks enhances productivity and quality in construction fabrication processes, ultimately contributing to the timely completion of construction projects.
Suggested article to read: AI or Artificial Intelligence in Project Management; 2024 Review
3. Laser Welding Robots
Laser welding robots are advanced tools that utilize high-powered lasers to join metal components with precision and efficiency. Here’s an overview of their characteristics and applications in construction:
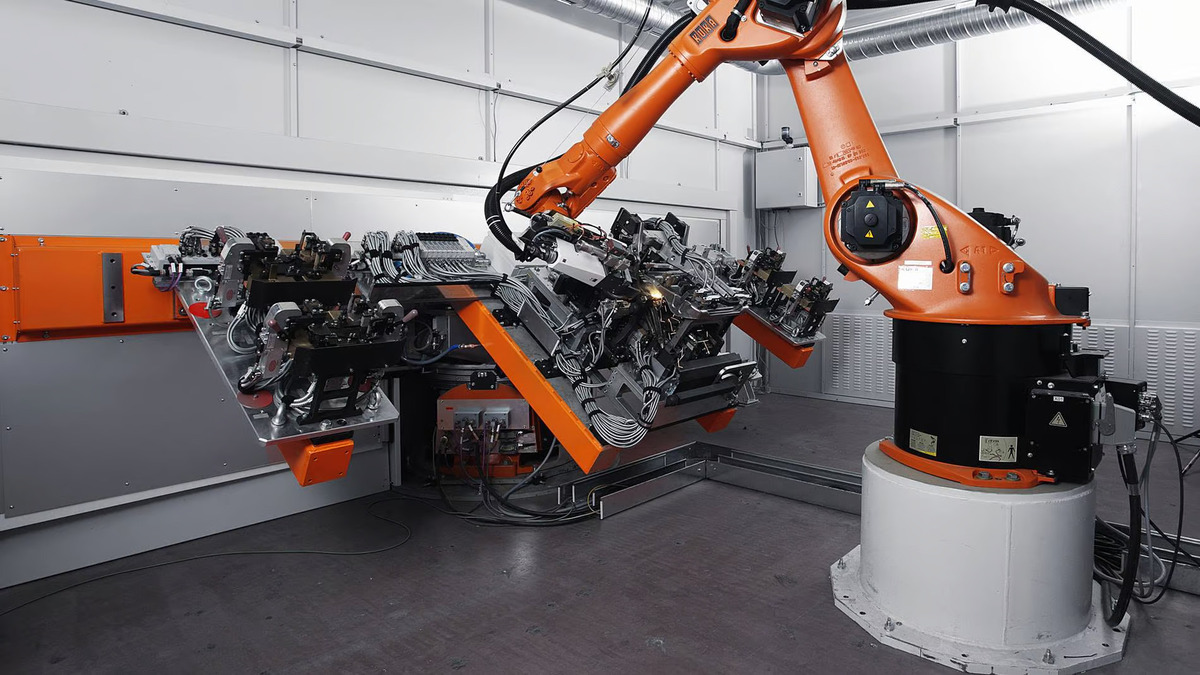
Characteristics:
- High Precision: Laser welding robots offer exceptional precision, allowing for narrow and focused weld seams. This precision is crucial in construction applications where accuracy is paramount, such as the fabrication of architectural metalwork and structural components.
- Minimal Heat Affected Zone (HAZ): Laser welding produces minimal heat input compared to traditional welding methods, resulting in a smaller heat-affected zone (HAZ) and reduced distortion of the workpiece. This characteristic is advantageous when welding thin materials or joining dissimilar metals.
- Versatility: Laser welding robots can be used with various materials, including carbon steel, stainless steel, aluminum, and even non-metallic materials like plastics and composites. They are suitable for welding complex geometries and can accommodate diverse construction requirements.
- High Speeds: Laser welding robots operate at high speeds, enabling rapid production cycles and increased throughput. This efficiency is particularly beneficial in construction projects where time is of the essence, such as the fabrication of building components and infrastructure elements.
- Contactless Operation: Unlike traditional welding methods that require physical contact between the welding electrode and the workpiece, laser welding is a contactless process. This eliminates the need for consumable electrodes and reduces the risk of contamination, resulting in cleaner and more precise welds.
Applications in Construction:
- Architectural Metalwork: Laser welding robots are utilized in the fabrication of architectural metalwork, including curtain walls, façade panels, decorative elements, and structural frameworks. Their ability to produce fine, aesthetically pleasing welds makes them well-suited for high-end architectural projects.
- Structural Steel Fabrication: In construction projects involving steel structures such as buildings, bridges, and stadiums, laser welding robots are used to join structural steel components with high accuracy and efficiency. They can weld beams, columns, trusses, and connections, ensuring the structural integrity of the final assembly.
- Aluminum Fabrication: Laser welding robots are particularly effective for welding aluminum components due to the material’s high reflectivity and thermal conductivity. They are employed in the construction of aluminum structures, façades, and architectural features where lightweight and corrosion-resistant materials are desired.
- Repair and Retrofitting: Laser welding robots can be used for repair and retrofitting tasks in construction, such as repairing damaged metal components or reinforcing existing structures with additional welds. Their precision and ability to work in confined spaces make them valuable assets for maintenance projects.
- Pipeline Welding: Laser welding robots are also utilized in construction projects involving pipelines and plumbing systems. They can weld metal pipes together with high precision, ensuring leak-proof joints and consistent weld quality in critical infrastructure installations.
Overall, laser welding robots offer construction companies a versatile and efficient solution for joining metal components with precision and reliability. Their advanced capabilities contribute to the quality, durability, and aesthetics of construction projects while optimizing production processes and reducing costs.
Suggested article to read: Artificial Intelligence or AI in Building; Guide to 2024
4. Plasma Cutting Robots
Plasma-cutting robots are essential tools in construction, offering precise and efficient cutting capabilities for a variety of materials. Here’s an overview of their characteristics and applications:
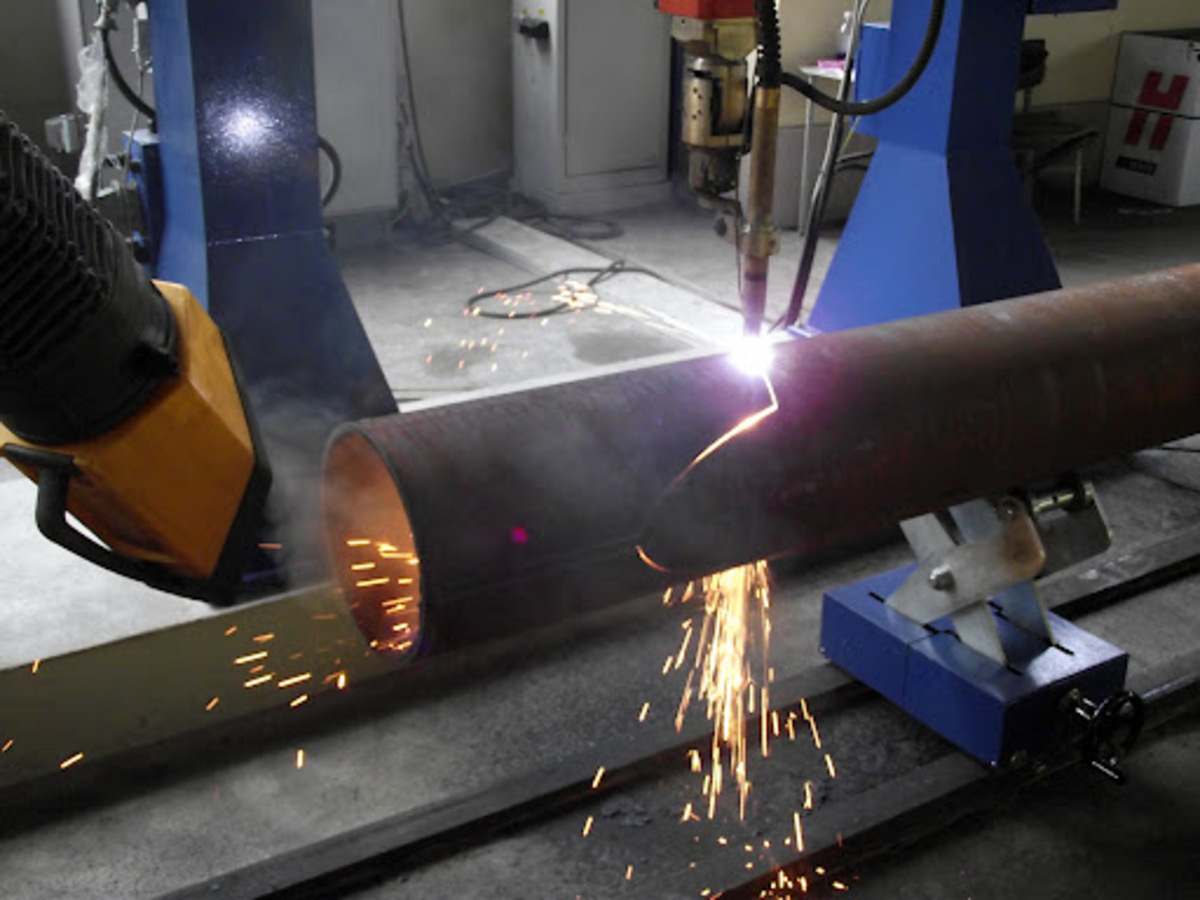
Characteristics:
- High Precision: Plasma-cutting robots offer excellent precision, allowing for clean and accurate cuts with minimal kerf width. This precision is crucial in construction applications where tight tolerances and intricate shapes are required.
- Versatility: Plasma-cutting robots can cut a wide range of materials, including carbon steel, stainless steel, aluminum, copper, and other conductive metals. They are suitable for cutting various thicknesses of materials, from thin sheets to thick plates, making them versatile tools for construction projects.
- High Speeds: Plasma-cutting robots operate at high speeds, enabling rapid cutting of materials and increased productivity. Their ability to perform intricate cuts quickly makes them ideal for fabrication processes where efficiency is essential.
- Clean Cutting: Plasma cutting produces clean, smooth edges with minimal dross and slag, reducing the need for secondary finishing operations. This characteristic is advantageous in construction applications where aesthetics and surface quality are important.
- Minimal Heat Affected Zone (HAZ): Plasma cutting generates less heat compared to other cutting methods, resulting in a smaller heat-affected zone (HAZ) and reduced distortion of the workpiece. This is particularly beneficial when cutting thin materials or heat-sensitive materials.
Applications in Construction:
- Structural Steel Fabrication: Plasma-cutting robots are widely used in the fabrication of structural steel components for buildings, bridges, and other infrastructure projects. They can cut beams, columns, plates, and other steel elements with precision and efficiency, meeting strict dimensional tolerances and design specifications.
- Sheet Metal Fabrication: In construction projects requiring sheet metal components such as panels, ductwork, and enclosures, plasma cutting robots are employed to cut metal sheets to size and shape. They can produce intricate cuts and contours accurately, facilitating the assembly of complex structures.
- Pipe Cutting: Plasma-cutting robots are utilized for cutting metal pipes and tubes in construction projects involving pipelines, plumbing systems, and HVAC (heating, ventilation, and air conditioning) installations. They can produce precise cuts with beveled edges, allowing for tight and leak-proof joints in piping systems.
- Demolition and Salvage: Plasma-cutting robots are also used in demolition and salvage operations to cut through metal structures, equipment, and debris. They can quickly dismantle and remove obsolete or damaged materials from construction sites, improving efficiency and safety in demolition projects.
- Artistic Metalwork: Plasma cutting robots are employed in the fabrication of artistic metalwork, sculptures, and decorative elements for architectural projects. They can cut intricate designs and patterns into metal sheets, creating custom-made features that enhance the aesthetics of buildings and public spaces.
Overall, plasma-cutting robots offer construction companies a versatile and efficient solution for cutting metal materials with precision and reliability. Their advanced capabilities contribute to the quality, speed, and cost-effectiveness of construction projects while meeting the diverse cutting requirements of modern construction applications.
Suggested article to read: Top 20 Construction AI Companies; 2024 Review
5. 3D Printing/Additive Manufacturing Robots
3D printing, also known as additive manufacturing, has gained significant traction in the construction industry due to its ability to produce complex structures with reduced material waste and faster construction times. Here’s how 3D printing robots are transforming construction:
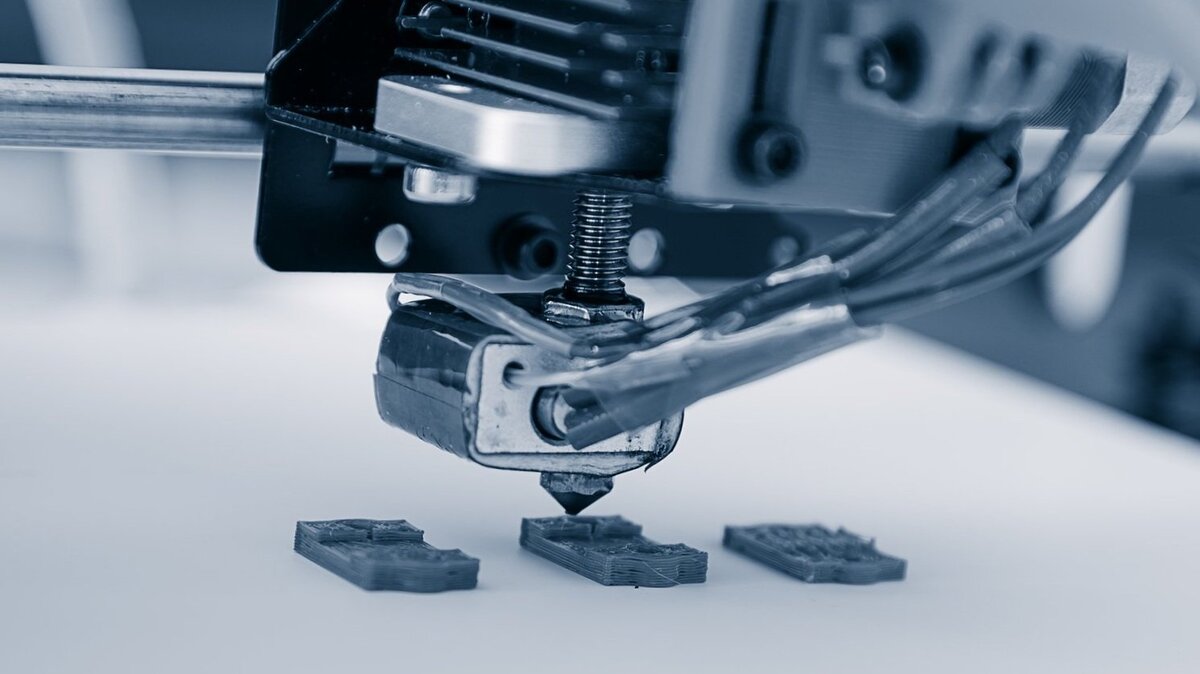
Characteristics:
- Layer-by-Layer Fabrication: 3D printing robots build structures layer by layer, depositing material according to digital design specifications. This additive process enables the creation of intricate geometries and customized components not feasible with traditional construction methods.
- Material Versatility: Additive manufacturing robots can work with various construction materials, including concrete, polymers, metals, and composite materials. This versatility allows for the fabrication of a wide range of structural elements, from concrete walls to metal connectors.
- Design Flexibility: 3D printing robots offer unparalleled design freedom, allowing architects and engineers to explore innovative designs and shapes. Complex geometries, organic forms, and intricate details can be easily realized, enabling the construction of unique and visually striking buildings.
- On-site Fabrication: Mobile 3D printing robots can be deployed directly to construction sites, enabling on-demand fabrication of building components. This eliminates the need for transporting prefabricated elements, reducing logistics costs and construction timelines.
- Customization: Additive manufacturing robots enable mass customization of building components, allowing each element to be tailored to specific project requirements. This customization extends to size, shape, material properties, and surface finish, accommodating diverse architectural visions and functional needs.
Applications in Construction:
- Building Components: 3D printing robots are used to fabricate various building components, including walls, columns, beams, and façade elements. These components can be printed off-site in controlled environments or directly on-site to integrate seamlessly into construction projects.
- Architectural Features: Additive manufacturing enables the creation of intricate architectural features such as decorative panels, ornamental details, and sculptural elements. These features can enhance the aesthetics of buildings and add unique character to architectural designs.
- Structural Elements: 3D printing robots are capable of producing load-bearing structural elements such as walls, slabs, and partitions. By optimizing material distribution and internal geometry, these elements can be lightweight yet structurally robust, offering new possibilities for sustainable construction.
- Infrastructure: Additive manufacturing is increasingly used in infrastructure projects to fabricate bridges, tunnels, retaining walls, and other civil engineering structures. 3D printing robots can create custom molds and formwork for casting concrete elements, streamlining construction processes and reducing labor costs.
- Emergency Shelter: In disaster relief scenarios or temporary housing projects, 3D printing robots can rapidly produce shelters and modular housing units on-site. These structures provide durable and cost-effective housing solutions for displaced populations, offering shelter and security in crisis situations.
Overall, 3D printing robots are revolutionizing construction by pushing the boundaries of design, efficiency, and sustainability. As the technology continues to evolve, it holds the promise of reshaping the built environment and unlocking new possibilities for architectural expression and construction innovation.
Suggested article to read: 13 Best AI Tools for Project Management in 2024
6. Automated Material Handling Robots
Automated material handling robots are essential components of modern construction sites, streamlining logistics, improving efficiency, and enhancing safety. Here’s an overview of their characteristics and applications:
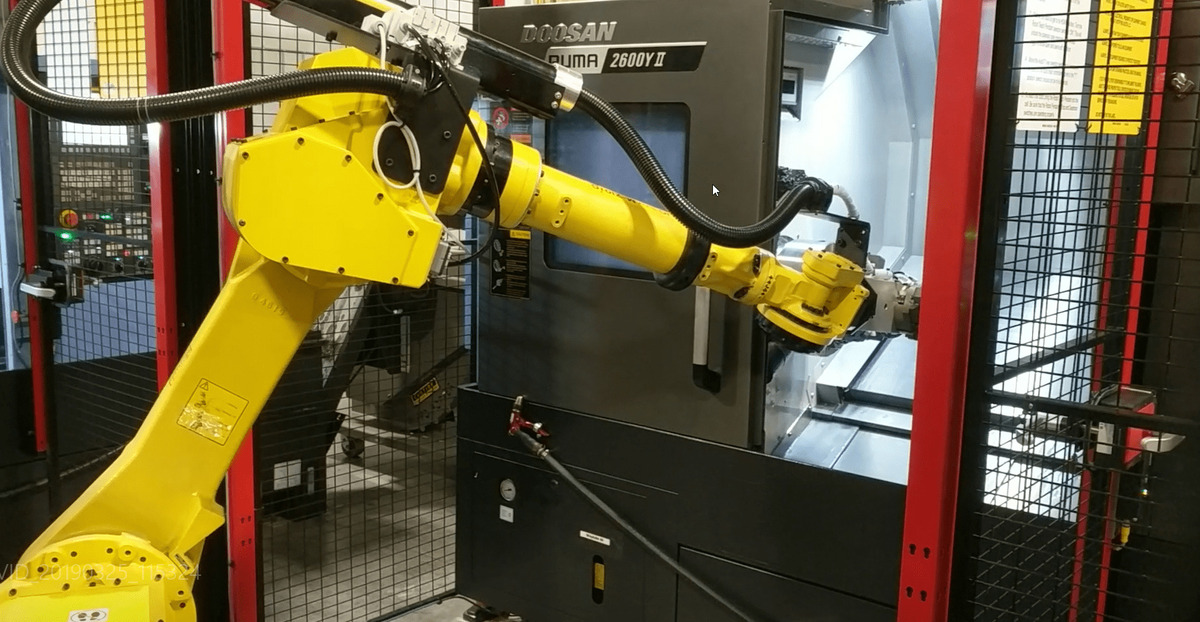
Characteristics:
- Versatility: Automated material handling robots are adaptable to various tasks, including loading, unloading, transporting, and positioning materials and components. They can handle a wide range of construction materials, such as steel beams, concrete panels, bricks, and piping.
- Precision: These robots offer precise control over material handling operations, ensuring accurate placement and alignment of components. This precision is crucial for maintaining quality standards and avoiding costly rework or delays in construction projects.
- Efficiency: Automated material handling robots operate continuously and can perform tasks around the clock, reducing downtime and improving overall productivity. Their ability to handle heavy loads and repetitive tasks with consistent speed and efficiency enhances construction site operations.
- Safety: By automating material handling tasks, these robots reduce the need for manual labor in potentially hazardous environments, improving workplace safety and minimizing the risk of accidents and injuries. They can operate in confined spaces, at heights, or in areas with limited access, mitigating safety concerns associated with manual handling.
- Integration: Automated material handling robots can be integrated with other construction machinery and systems, such as cranes, conveyor belts, and robotic fabrication cells. They can communicate with centralized control systems to optimize workflow coordination and material flow throughout the construction site.
Applications in Construction:
- Material Transport: Automated material handling robots are used to transport materials and components from storage areas to designated work zones on construction sites. They can navigate through complex environments, including uneven terrain, narrow passageways, and crowded spaces, to deliver materials efficiently.
- Palletizing and Stacking: These robots can palletize building materials such as bricks, blocks, tiles, and bags of cement, stacking them neatly for storage or transportation. They can also depalletize materials as needed for assembly or installation processes, minimizing manual handling and reducing labor costs.
- Assembly Line Operations: In prefabrication facilities or modular construction settings, automated material handling robots play a crucial role in assembling prefabricated components and modules. They can sequence and coordinate assembly line operations, ensuring smooth production flows and timely completion of prefabricated elements.
- Waste Management: Automated material handling robots are utilized in construction waste management processes, such as sorting, recycling, and disposal. They can segregate recyclable materials, transport debris to designated collection points, and assist in waste compaction and disposal activities, promoting sustainability and environmental stewardship on construction sites.
- Equipment Maintenance: These robots can also be used for transporting tools, equipment, and spare parts to maintenance crews working on construction machinery and vehicles. By automating material delivery tasks, they improve the efficiency of equipment servicing and reduce downtime associated with manual retrieval of tools and supplies.
Overall, automated material handling robots play a critical role in optimizing material flow, enhancing productivity, and ensuring safety on construction sites. As construction technology continues to advance, these robots will likely become even more integral to the efficient and sustainable delivery of construction projects.
Suggested article to read: Building Automation System (BAS): Ultimate Guide for 2024
7. Robotic Rebar Processing and Placement
Robotic rebar processing and placement systems are revolutionizing the way reinforcement bars (rebar) are handled, cut, bent, and installed in construction projects. Here’s an overview of their characteristics and applications:
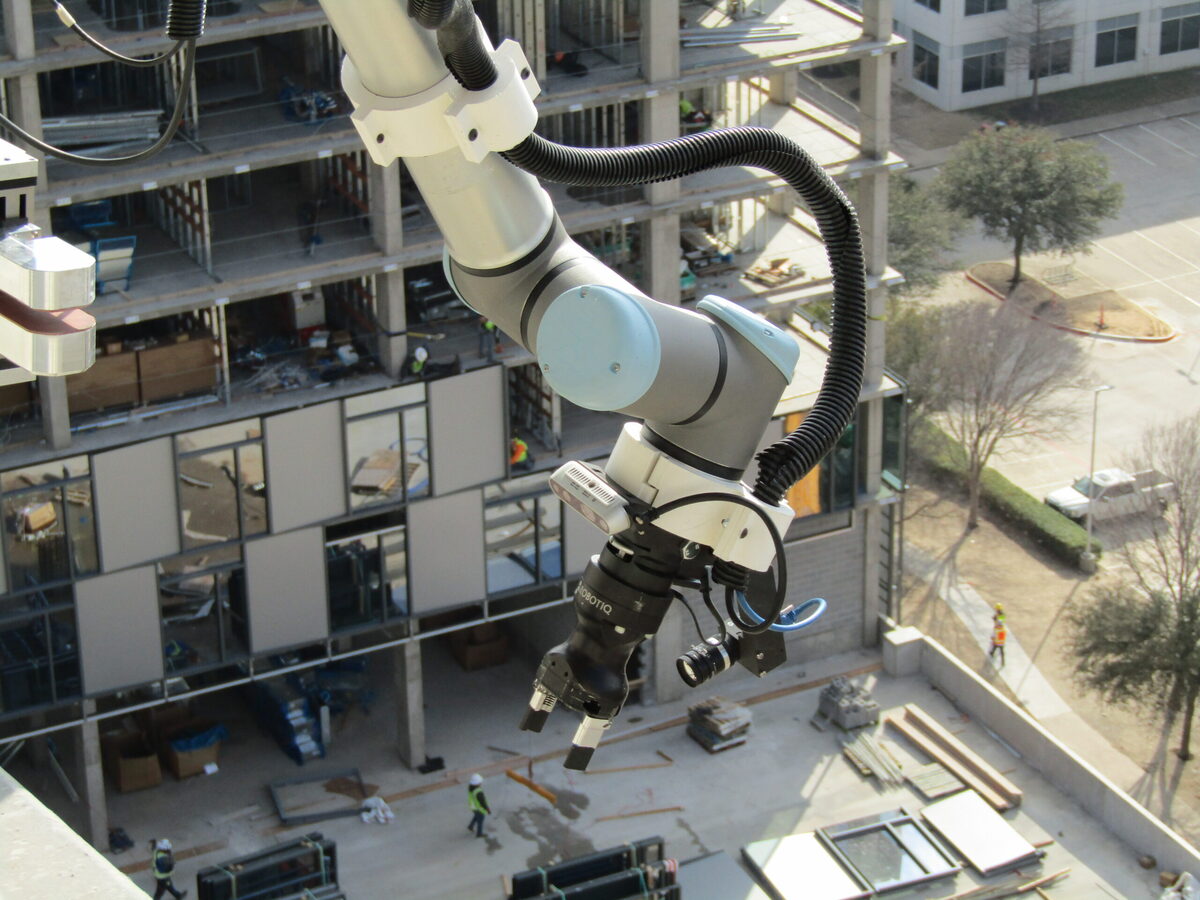
Characteristics:
- Automation: Robotic rebar processing and placement systems automate repetitive and labor-intensive tasks involved in handling and shaping reinforcement bars. These systems can be programmed to precisely cut, bend, and assemble rebar according to construction drawings and specifications.
- Precision: These robots offer high precision in cutting and bending rebar, ensuring that each bar meets exact dimensional requirements. This precision helps to minimize material waste, optimize reinforcement layouts, and enhance the structural integrity of concrete elements.
- Flexibility: Robotic rebar processing systems are versatile and can handle various rebar sizes, shapes, and configurations. They can accommodate complex reinforcement patterns and adapt to changes in design or construction requirements with minimal reprogramming or setup time.
- Speed: By automating rebar processing tasks, these systems significantly increase productivity and reduce construction timelines. They can perform tasks such as cutting, bending, and assembling rebar much faster than manual methods, accelerating the construction process.
- Integration: Robotic rebar processing and placement systems can be integrated with other construction machinery and equipment, such as concrete pumps, formwork systems, and crane systems. This integration enables seamless coordination of reinforcement installation with other construction activities, optimizing workflow efficiency.
Applications in Construction:
- Rebar Cutting and Bending: Robotic rebar processing systems are used to automatically cut rebar to specific lengths and bend them into required shapes, such as stirrups, hooks, and beams. These systems ensure consistent quality and accuracy in rebar fabrication, reducing errors and rework during construction.
- Prefabrication: In prefabricated construction methods, robotic rebar processing systems are utilized to fabricate pre-made rebar cages, mats, and assemblies off-site. Prefabricated rebar elements can then be transported to construction sites and installed quickly, streamlining construction processes and reducing on-site labor requirements.
- On-Site Installation: Robotic rebar placement systems are deployed on construction sites to automate the installation of rebar within concrete structures. These systems can accurately position rebar according to design specifications, ensuring proper reinforcement coverage and alignment before concrete placement.
- Tunneling and Infrastructure Projects: In tunneling and infrastructure projects, robotic rebar processing and placement systems are used to reinforce concrete structures such as tunnels, bridges, dams, and underground utilities. These systems help to improve the durability and longevity of infrastructure assets by ensuring reliable reinforcement installation.
- High-Rise Construction: In high-rise buildings and skyscrapers, robotic rebar processing systems play a crucial role in reinforcing concrete columns, walls, and floor slabs. These systems can handle the high volume of rebar required for tall structures efficiently, contributing to the structural stability and safety of the building.
Overall, robotic rebar processing and placement systems offer construction companies a highly efficient and accurate solution for handling and installing reinforcement bars in concrete structures. By automating rebar fabrication and installation tasks, these systems improve productivity, quality, and safety on construction sites, ultimately leading to faster project delivery and enhanced structural performance.
Suggested article to read: AI for Construction Vehicle Automation: Neural Networks and Machine Learning Approaches
Conclusion
In the dynamic landscape of construction, the integration of robotic welding and fabrication technologies stands as a transformative force, revolutionizing traditional methods with efficiency, precision, and safety. Across a spectrum of applications, from structural steel fabrication to intricate sheet metal work, robotic systems have become indispensable tools, offering versatility and reliability unmatched by manual labor alone.
Arc welding robots, with their adaptability to various welding processes and seamless integration into production lines, have become the backbone of structural fabrication in construction projects. Their precision and efficiency ensure the quality and durability of welded components, from beams and columns to intricate pipe joints.
Spot welding robots, prized for their ability to apply localized heat and pressure with consistency and speed, have become essential for assembling sheet metal components in construction. From prefab construction to automotive manufacturing, these robots deliver reliable welds, meeting the demands of high-volume production with ease.
Laser welding robots, with their unparalleled precision and minimal heat-affected zones, have found niche applications in architectural metalwork and structural steel fabrication. Their ability to produce clean, aesthetically pleasing welds aligns perfectly with the demands of high-end construction projects.
Plasma-cutting robots, renowned for their versatility and efficiency, have become indispensable for cutting metal materials with precision and reliability. From structural steel components to intricate artistic metalwork, these robots deliver clean cuts, meeting the diverse cutting requirements of modern construction projects.
Furthermore, the emergence of 3D printing and automated material handling robots further expands the horizons of construction fabrication, offering innovative solutions for complex architectural elements and streamlined material handling processes.
As robotic welding and fabrication technologies continue to evolve, they promise to reshape the construction industry, driving productivity, quality, and safety to new heights. Embracing these advancements opens doors to a future where construction projects are executed with unparalleled efficiency and precision, laying the foundation for a built environment that is both functional and aesthetically inspiring.
Suggested article for reading:
10 Best Construction AI Software in 2024
Artificial Intelligence or AI in Construction Industry; Guide to 2024
Resources:
Universal Robots | WEvolver | Robycs Technology | Novatr | Inrotech | Peddinghaus | Springer | MDPI | Cyber-Weld
For all the pictures: Freepik | KUKA | Kiberys | Tronix3D | Acieta | zacoua venture